There has been a long old tradition of using vacuum systems to hold the substrates while using Spin Coaters. Nonetheless researchers prefer the vacuum less solution too considering the limitations of the vacuum option. This has made the researchers put a check on the shape and size of the substrates while using the vacuum-less Spin Coaters.
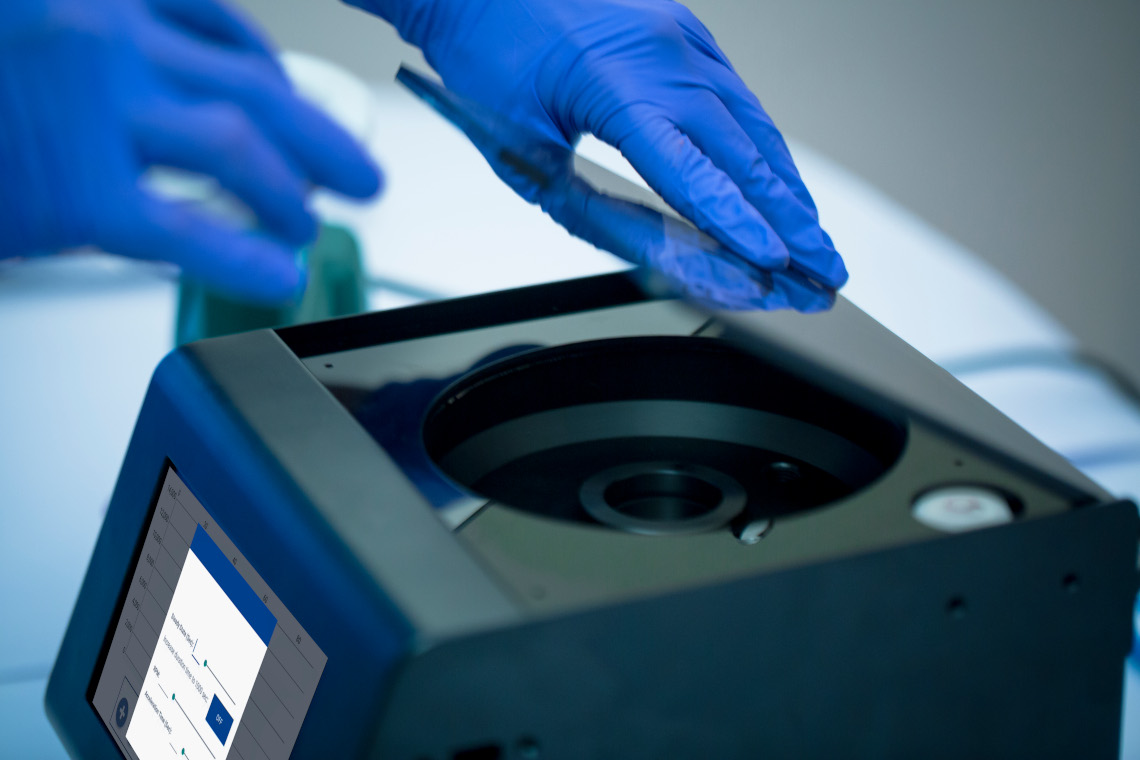
Vacuum-Less Spin Coaters…
So, what are the advantages and disadvantages of using Vacuum-Less options?
Can achieve RPM greater than 12000
Prevents the formation of central deformation
Standalone device without the use of any supporting device
Glove Box friendly
Instant startup and run. No setup time.
Difficult to accommodate irregular substrates
Possibility of splash back
Few of the researchers working on thin films use flexible substrates. When Spin Coating these substrates on a vacuum-based spin coater, they often observe that there exists a central depression which causes the solution to flow down and concentrate in the middle. This makes the coating lose its uniformity.
The advantage of making the instrument a standalone device a attracted many experimentalists because it is easy to install the equipment in either a vacuum chamber or a fume hood with no other moving parts except the instrument itself. Though there have been developments to use the oil-free vacuum pumps to avoid contamination of the fume-hood/vacuum chamber, it is advised to use the vacuum-free model.
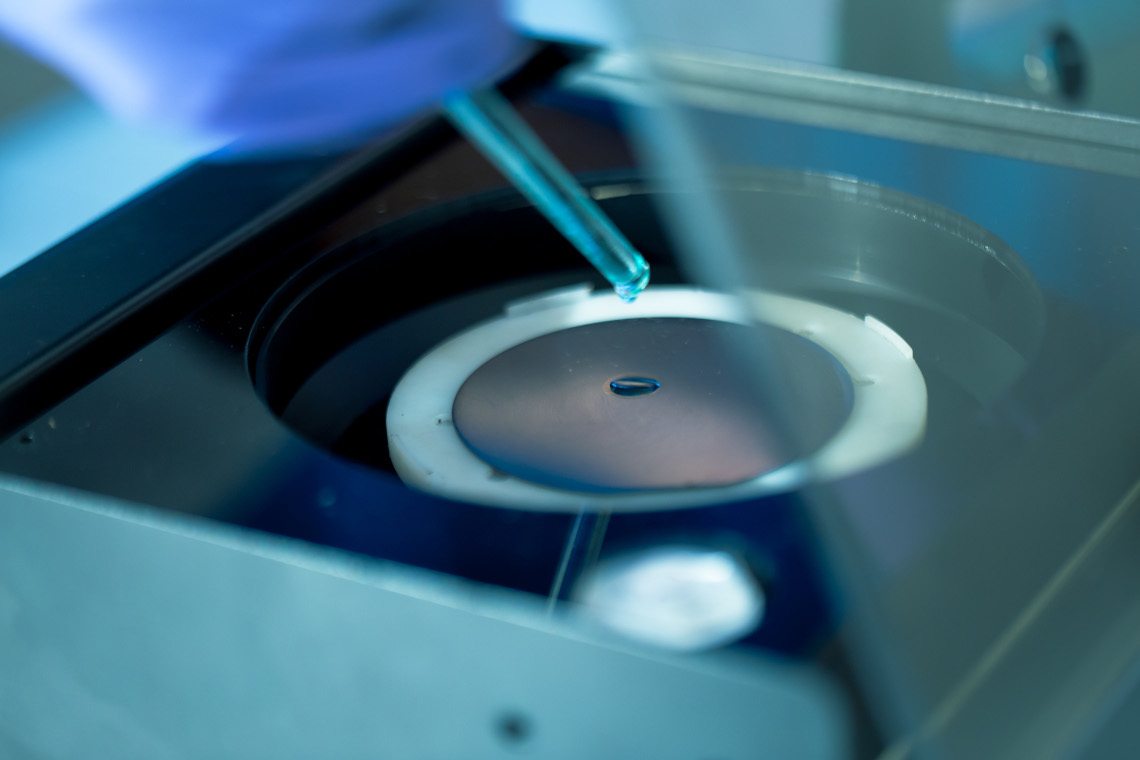
In general, when researchers think about using the vacuum-less model, the first thing that comes to their mind is the irregular shapes and sizes of the substrates. This comes from the fact that some substrates are sold as standard sized wafers which are costly. It is economical and financially efficient to break them down to smaller pieces for experiments. This being the case, if the substrates are broken down in a roughly same manner each time, it can still be accommodated on a groove type chuck.